COMPRESSION TEST
The compressive strength of Concrete is the most common performance measure to determine the strength of concrete for designing.This is measured by breaking cubical of cylindrical concrete specimen in Compression Testing Machine.
AIM
To determine the compressive strength of concrete specimens as per IS: 516 - 1959.
To determine the compressive strength of concrete specimens as per IS: 516 - 1959.
APPARATUS
AGE AT TEST
Tests should be done at recognized ages of the test specimens, usually being 7 and 28 days. The ages should be calculated from the time of the addition of water to the drying of ingredients.
Tests should be done at recognized ages of the test specimens, usually being 7 and 28 days. The ages should be calculated from the time of the addition of water to the drying of ingredients.
NUMBER OF SPECIMENS
At least three specimens, preferably from different batches, should be taken for testing at each selected age.
At least three specimens, preferably from different batches, should be taken for testing at each selected age.
PROCEDURE
i) The specimens, prepared according to IS: 516 - 1959 and stored in water, should be tested immediately on removal from the water and while still in wet condition. Specimens when received dry should be kept in water for 24hrs. before they are taken for testing. The dimensions of the specimens, to the nearest 0.2mm and their weight should be noted before testing.
ii) The bearing surfaces of the compression testing machine should be wiped clean and any loose sand or other material removed from the surfaces of the specimen, which would be in contact with the compression platens.
iii) In the case a of cubical specimen, the specimen should be placed in the machine in such a manner that the load could be applied to the opposite sides of the cubes, not to the top and the bottom. The axis of the specimen should be carefully aligned with the centre of thrust of the spherically seated platen. No packing should be used between the faces of the test specimen and the steel platen of the testing machine. As the spherically seated block is brought to rest on the specimen, the movable portion should be rotated gently by hand so that uniform seating is obtained.
iv) The load should be applied without shock and increased continuously at a rate of approximately 140kg/sq.cm/minute until the resistance of the specimen to the increasing load breaks down and no greater load can be sustained. The maximum load applied to the specimen should then be recorded and the appearance of the concrete and any unusual features in the type of failure should be noted.
i) The specimens, prepared according to IS: 516 - 1959 and stored in water, should be tested immediately on removal from the water and while still in wet condition. Specimens when received dry should be kept in water for 24hrs. before they are taken for testing. The dimensions of the specimens, to the nearest 0.2mm and their weight should be noted before testing.
ii) The bearing surfaces of the compression testing machine should be wiped clean and any loose sand or other material removed from the surfaces of the specimen, which would be in contact with the compression platens.
iii) In the case a of cubical specimen, the specimen should be placed in the machine in such a manner that the load could be applied to the opposite sides of the cubes, not to the top and the bottom. The axis of the specimen should be carefully aligned with the centre of thrust of the spherically seated platen. No packing should be used between the faces of the test specimen and the steel platen of the testing machine. As the spherically seated block is brought to rest on the specimen, the movable portion should be rotated gently by hand so that uniform seating is obtained.
iv) The load should be applied without shock and increased continuously at a rate of approximately 140kg/sq.cm/minute until the resistance of the specimen to the increasing load breaks down and no greater load can be sustained. The maximum load applied to the specimen should then be recorded and the appearance of the concrete and any unusual features in the type of failure should be noted.
CALCULATION
The measured compressive strength of the specimen should be calculated by dividing the maximum load applied to the specimen during the test by the cross - sectional area, calculated from the mean dimensions of the section and should be expressed to the nearest kg/sq.cm. An average of three values should be taken as the representative of the batch, provided the individual variation is not more than ±15% of the average. Otherwise repeat tests should be done.
A correction factor according to the height/diameter ratio of the specimen after capping should be obtained from the curve given below:-
The measured compressive strength of the specimen should be calculated by dividing the maximum load applied to the specimen during the test by the cross - sectional area, calculated from the mean dimensions of the section and should be expressed to the nearest kg/sq.cm. An average of three values should be taken as the representative of the batch, provided the individual variation is not more than ±15% of the average. Otherwise repeat tests should be done.
A correction factor according to the height/diameter ratio of the specimen after capping should be obtained from the curve given below:-
The product of this correction factor and the measured compressive strength is known as the corrected compressive strength, this being the equivalent strength of a cylinder having a height/diameter ratio of two. The equivalent cube strength of the concrete should be determined by multiplying the corrected cylinder strength by 1.25.
REPORTING OF RESULTS
The following information should be included in the report on each test specimen:
i) Identification mark
ii) Date of test
iii) Age of specimen
iv) Curing conditions, including date of manufacture of specimen
v) Weight of specimen
vi) Dimensions of specimen
vii) Cross-sectional area
viii) Maximum load
ix) Compressive strength
x) Appearance of fractured faces of concrete and type of fracture, if unusual.
The following information should be included in the report on each test specimen:
i) Identification mark
ii) Date of test
iii) Age of specimen
iv) Curing conditions, including date of manufacture of specimen
v) Weight of specimen
vi) Dimensions of specimen
vii) Cross-sectional area
viii) Maximum load
ix) Compressive strength
x) Appearance of fractured faces of concrete and type of fracture, if unusual.
Concrete
Definition-Concrete is a mixture of cement,sand(Fine Aggregates),pebbles or crushed rock(coarse aggregates) and water, which when placed in the skeleton of forms and allowed to cure, becomes hard like stone.
Properties of Cement Concrete.
ii) The shrinkage of cement concrete occurs in hardness.
7. Concrete forms a hard surface Capable of resisting abrasion.
8. Its final strength and quality mainly depends on handling and local conditions.
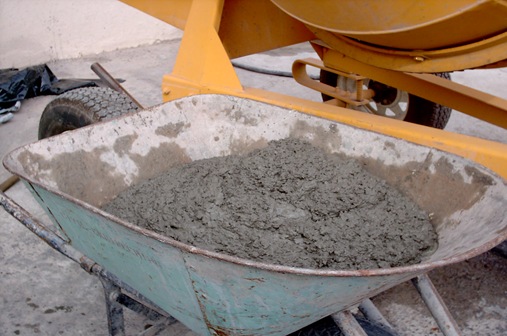
Concrete
Properties of Cement Concrete.
- It has a high compressive strength.
- It is free from corrosion and there is no applicable effect of atmospheric agents on it.
- It hardens with its age and process of hardening goes for a long time after concrete has obtained its sufficient strength.
- It is more economical than steel.
- It binds with steel rapidly and creates a very good bond. As concrete is weak in tension the steel reinforcement placed in concrete takes up the tensile strength. This is termed as RCC.
- Under the following conditions is has a tendency to shrink.
ii) The shrinkage of cement concrete occurs in hardness.
7. Concrete forms a hard surface Capable of resisting abrasion.
8. Its final strength and quality mainly depends on handling and local conditions.
Concrete
Various Lab Test On Concrete
There are many tests which are conducted to check the quality of concrete. These tests are basically divided into two categories
1. Various Lab Test On Fresh Concrete.a) Slump Test – Workability
b) Compacting Factor
c) Vee- Bee Test
2.Various Lab Test On Hardened Concrete.
There are two kinds of tests which are done on hardened concrete. These are non destructive test and destructive tests. In non destructive test, the sample is not destroyed and this test is very useful in determining the strength of existing buildings or structures where as in destructive test a sample is made and then destroyed to find out the strength of concrete.Compression test is the example of destructive test. Here are the nondestructive tests.
a) Rebound Hammer Testb) Ultrasonic Pulse Velocity Test
Ductal- A Stronger Concrete
What is Ductal?
Few Years back in 2006; researchers at Iowa State University have developed a new type of concrete that is much stronger than conventional concrete. It can withstand pressures up to 595,000 pounds — more than the weight of seven semi trucks.
A new kind of concrete called Ductal that might allow bridges to hold more weight and last longer. Although it is 10 times more expensive than traditional materials but stronger and virtually impermeable, helping bridges become more durable.
The researchers conducted a load-bearing capacity test using a 71-foot beam made out the new concrete. They applied increasing amounts of hydraulic pressure to the top of the beam to see how much it could withstand before breaking. It finally broke with a loud pop at 595,000 pounds. The ultra-high performance concrete is made from sand, cement, water and small steel fibers. Standard concrete uses coarser materials. The new concrete is specifically engineered to include finer materials and steel fibers, making it denser and stronger.
This comment has been removed by the author.
ReplyDelete